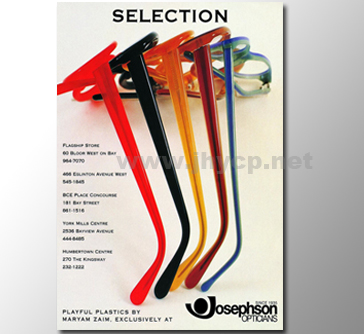
主要原因:
1、油墨的成膜劑不足
2、油墨體系顏料過量尤其是體系顏料過人,太粗而使流體有脹流;
3、油墨粉體物過多墨質(zhì)粗,墨膜軟而不堅;
4、油墨體系的PH值過高;
5、油墨泡沫過大(尤其是高速輪轉(zhuǎn)印刷摩擦后導(dǎo)致的油墨溫度過高而產(chǎn)生的墨表面泡沫的形成);
6、紙張質(zhì)量差(粗糙、疏松),表面塵埃度大/塑料薄膜吸濕而降低了附著力;
7、油墨吸入了水份,包括塑料薄膜吸入水份;
8、承印載體水份過大/塑料薄膜未處理或處理的不好或塑料表面油膩含量大/塑料體系的助劑遷移到表面;
9、油墨體系的助溶劑過量,尤其是非揮發(fā)性,非混性的溶劑過多或油墨干后表面發(fā)澀;
10、印刷后半部干燥設(shè)施不當(dāng);
11、油墨太稀或附著牢度差,油墨膠化絮凝或鹽析,連結(jié)料已失去了粘結(jié)作用;
12、油墨混入雜質(zhì)和水份而堆版或酸敗分解;
13、油墨分散(包括印刷傳墨輥)不良式?jīng)_洗不良;
14、印壓不實或輥子功能不良或墊襯不足;
15、油墨干性太慢,連結(jié)料質(zhì)量太次而又大量滲入了承印載體(如紙吸取性太快)太深;尤其是當(dāng)摩擦,折疊打包或消費過程更為明顯;
16、刷墨及印刷油墨液偏酸;
17、印刷速度不合適(太快);
18、印壓大小;
19、承印載體與橡皮布或與印版之間附著紙、塑毛、粉塵,油墨中加入的撤粘劑過量。
二、措施方法
1、控制環(huán)境溫度和濕度(18-25℃和60-75%);
2、加大吹風(fēng),烘干,防止墨膜干后發(fā)脆;
3、選擇密度大,緊度高的紙張和處理形成的塑料毛面(如施膠量大的紙張/吸收性稍弱一點)及選擇水、墨分離而又平整的印版;
4、控制紙張水分(4-14%);
5、控制承印性的PH值;
6、調(diào)整印刷壓和承印物拉力(尤其是印版的彈性);
7、增大曝光時間并控制曝光量;
8、更換印刷油墨或在油墨中加入一些稠、粘的連結(jié)料或提高印刷壓力或換用優(yōu)質(zhì)的紙或PH值小的紙張;
9、用紅外線碘鎢燈升溫復(fù)打電暈處理并糾正電暈面或重新進(jìn)行表面處理;
10、在塑料薄膜中添加蠟類或鈣或換用紙張;
11、油墨中添加偶聯(lián)劑或防滲劑和添加增粘劑或選擇適宜的成膜助劑;
12、選擇粘性大的或適當(dāng)細(xì)度的油墨或過濾油墨;
13、控制油墨的PH值(7-9.3)及選擇硬質(zhì)的油墨;
14、控制油墨干速(例如輪轉(zhuǎn)水性凹印油墨1-3秒內(nèi)表面干燥)�;驌Q用干速較快的油墨或減少給墨量;
15、設(shè)計調(diào)配揮發(fā)或氧化梯度平衡的溶劑或調(diào)量油或盡量調(diào)配粘度高的油墨;
16、改進(jìn)油墨連結(jié)料的結(jié)構(gòu)及稠度(如采用非反應(yīng)的樹脂與亞麻油、熟油或中等粘度的調(diào)墨油);
17、使用能迅速干燥的包裝印刷油墨,在油墨中加入少量的罩光油或亮光油(如設(shè)法改性油墨干性,摻用對顏料和紙張粘附性的好的油墨,比重小、吸油量大的顏填料),使用弱堿性潤濕液;
18、不要把油墨調(diào)得太稀,加入一些蠟類增滑劑,換用附著牢度好的油墨(選擇同性同能的油墨)或罩層樹脂油或覆合一層塑料薄膜;
19、油墨中的樹脂顏料比例要適當(dāng)(或選擇分子量大的樹脂,比重大而少的顏料或填料加入增塑劑;盡量減少噴粉(如油墨中加入玉米淀粉或滑石粉,盡可用325-400目篩網(wǎng)過濾后再用);
20、選用彈性好的橡皮布和在印版墊支附加彈性的又光滑平整的橡皮或塑料泡沫。盡量減少撤粘劑。
|